Laboratory for Cognitive systems in Logistics
The focus of our basic research work is the development of analytical and numerical models for the analysis and optimisation of modern material handling system solutions with an emphasis on storage and robotic order-picking systems.
In applied research, we are involved in the development and design of prototypes for material handling and storage technology, the development of sensor systems in material handling and the logistical analysis of material flow in intralogistics.
Laboratory’s basic and applied research work is based on the following main areas:
An important area of logistics is intralogistics or internal logistics, which includes all technical systems, services and related activities that have to do with the in-plant material flow of production companies. Intralogistics processes are crucial for managing the flow of goods along the entire supply chain, as they ensure the reliable and predictable flow of physical goods in the nodes of a supply network.
The research area of intralogistics covers the planning, modelling and multi-criteria optimisation of transport, storage and order-picking processes with regard to maximum throughput capacity, minimum operating costs, energy efficiency and sustainability. In particular, the development of advanced relocation and storage strategies in multi-deep storage systems is the focus of our work.
Analytical and numerical models are used to perform cycle time analysis, throughput and energy efficiency analyses for the planning, design and implementation of intralogistics systems. For more advanced logistics systems, we use multi-objective optimisation of decision variables in multiple objective functions in intralogistics by using the software MatLab.
For our own research projects in intralogistics, several computer-based tools have been developed and used, such as DeSklad for planning automated warehouses, software in MS Excel using Visual Basic for shuttle simulation, and a special software OptiMax for optimising discrete logistics systems, etc.
In the research field of intralogistics two PhD dissertations:
- “Development of relocation strategies in a multi-deep automated vehicle storage and retrieval system” and
- “Design and optimization model of distinctively heavy and long unit loads AS/RS”
have been registered and approved by the University of Maribor doctoral school.
We pass on our knowledge from the research field of intralogistics not only to our research partners but also to the industry. Recently, we have carried out many industry cooperation in the context of material flow simulation from production and logistics planning to storage and order-picking systems.
With the beginning of e-commerce, new generations of warehouses have emerged that specialize in the specific needs of online business-to-consumer (B2C) retailers. The statistics portal Statista (“Global retail e-commerce market size 2014-2023,” 2019) shows that in 2019 the global online sales market amounted to 3.535 million USD and is projected to continue to grow in the coming years (Figure 1).
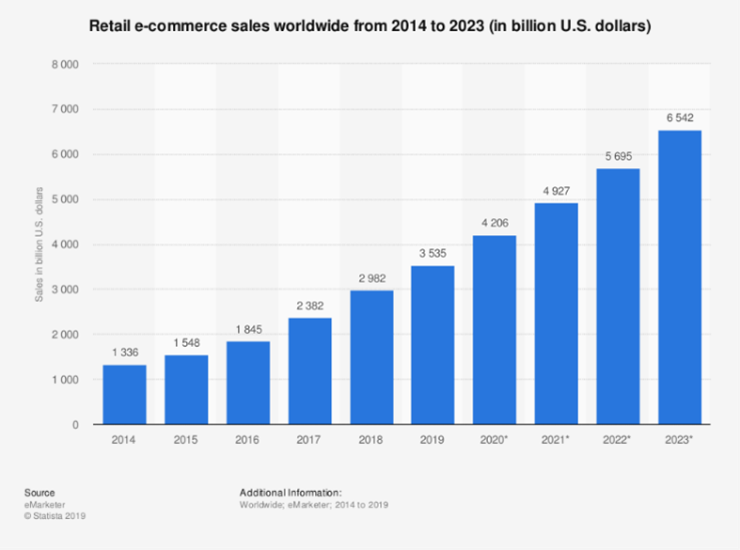
Source: https: //www.statista/ statistics/ 379046 /worldwide-retail-e-commerce-sales/
E-commerce and their warehouses are facing the following requirements: small size orders, large product assortment, short delivery times, and variable order quantity. Conventional warehouses have difficulty on meeting these requirements. One of the most labour-intensive and demanding processes in warehouses (both automated and non-automated) is the order-picking process, which is usually non-automated or only partially automated. The order-picker often suffers from poor ergonomics in the workplace and with demands for high precision work, which usually takes place in multiple work shifts. Due to the above, automation and robotization of warehousing processes are certainly key factors in warehouses of the future, where we see a great potential for progress (Figure 2).
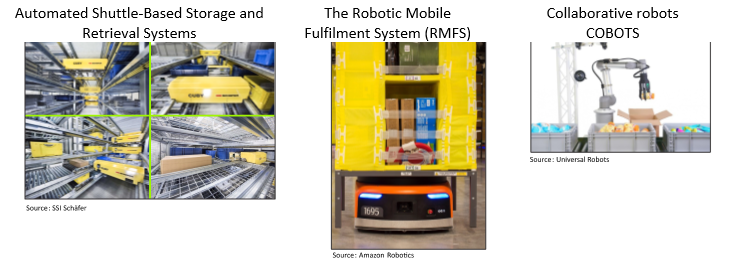
Source: SSI Schäfer, Amazon Robotics, Universal Robots.
A major trend in the application of collaborative robotics in logistics is evident in the field of robotic bin picking. Due to the large assortment of items (different dimensions, shapes, weights, etc.), order-picking is difficult to robotize, therefore this process is still largely dependent on human order-pickers. With the development of collaborative robotics, advanced robotic grippers, 3D machine vision, machine and deep learning algorithms, new order-picking possibilities appear.
Research area in collaborative robotics is focusing on the development of new object recognition algorithms, positioning and orientation of objects within storage manipulation units and optimal object gripping algorithms by using different robotic gripping devices (two-fingers, vacuum, gecko, etc.).
In the research field of “Collaborative robotics in logistics” a PhD dissertation entitled: “Optimal selection of robotic gripper for robotic bin-picking in automated storage systems” has been registered and approved by the University of Maribor doctoral school.
Warehousing is one of the most important activities in the supply chain, enabling competitive advantage. Effective management of warehousing processes is, therefore, crucial for achieving minimal costs, maximum efficiency, and overall customer satisfaction. Warehouse Management Systems (WMS) are the first steps towards organizing these processes; however, due to the human factor involved, information on products, vehicles and workers may be missing, corrupt, or misleading.
The research area in sensor systems in logistics is focusing on the development of various sensor systems connected to the Internet of Things (IoT), which enable the connection of multiple objects in the supply chain.
Our developed cost-effective Indoor Positioning System (IPS) based on Bluetooth Low Energy (BLE) works automatically and therefore minimizes the possibility of acquiring incorrect data (Figure 1). The proposed IPS solution is intended to be used for supervising order-picker movements, movement of packages between workstations, and tracking other mobile devices in a manually operated warehouse.
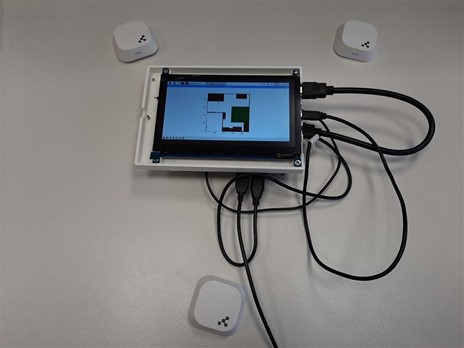
Source: own
Another research area in this field is developing the assisted “Pick-to-Light assembly systems” that guide the assembler through the assembly steps of highly complex and individual parts. Our developed prototype “Pick-to-Light assembly systems” is supported by a “Machine vision system” that monitors and checks the assembly parts before being assembled together, which provides high productivity in the assembly process.
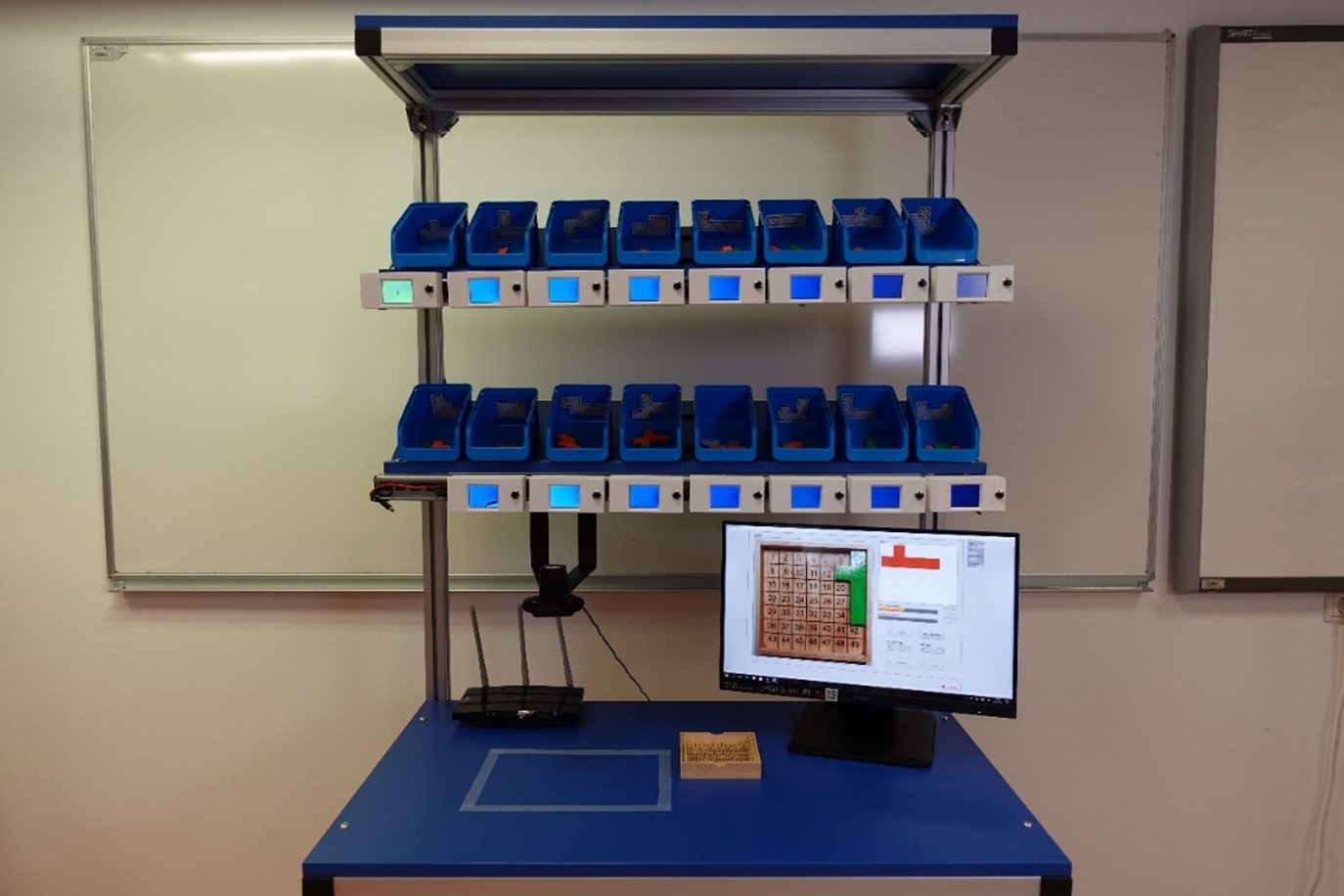
Source: own
The core competencies of logistics technology lie in the development and modelling of prototypes for material handling and storage technology with the help of analytical methods and computer-aided (virtual) tools such as SolidWorks and MSC Adams.
Most recent research project from “Logistics technique and technology” relate to:
Planning, development and design of Shelf Carrier System for mobile robot MiR 100
In the framework of the research field “Logistics technique and technology” and in collaboration with students, a Shelf Carrier System for the mobile robot MiR 100 has been developed, designed and constructed.
Source: own
Source: own
Planning, development and design of Anchoring System for mobile robot MiR 100
In the framework of the research field “Logistics technique and technology” and in collaboration with students, an Anchoring System for the mobile robot MiR 100 has been developed and designed.
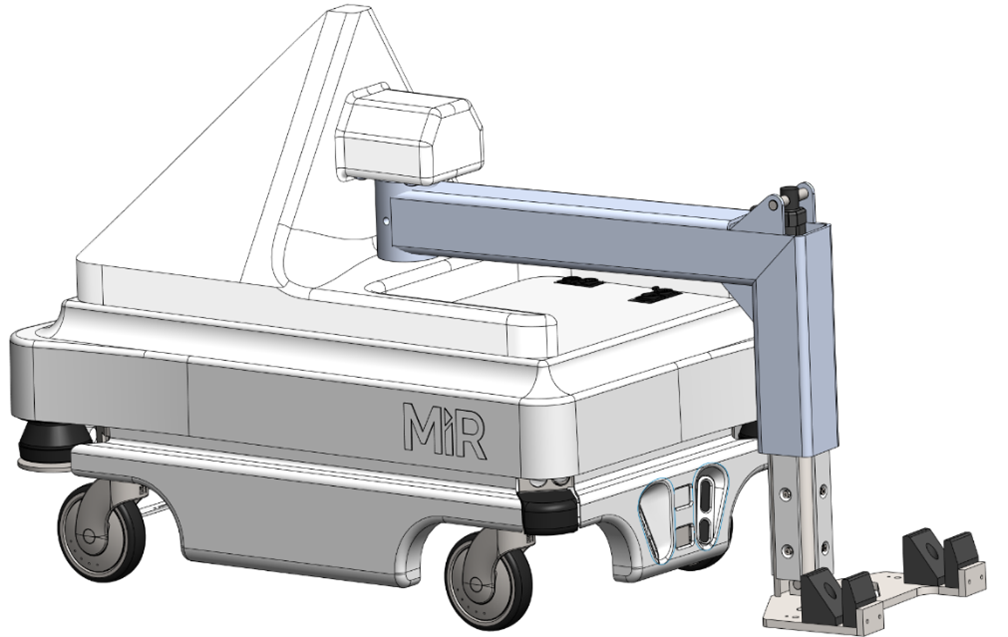
Source: own
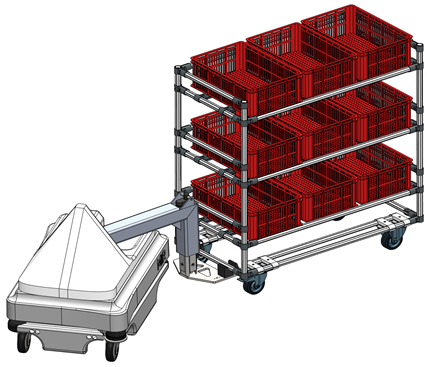
Source: own
Planning, development and design of Lifting-conveyor System for mobile robot MiR 100
In the framework of the research field “Logistics technique and technology” and in collaboration with students, a Lifting-conveyor System for the mobile robot MiR 100 has been developed and designed.
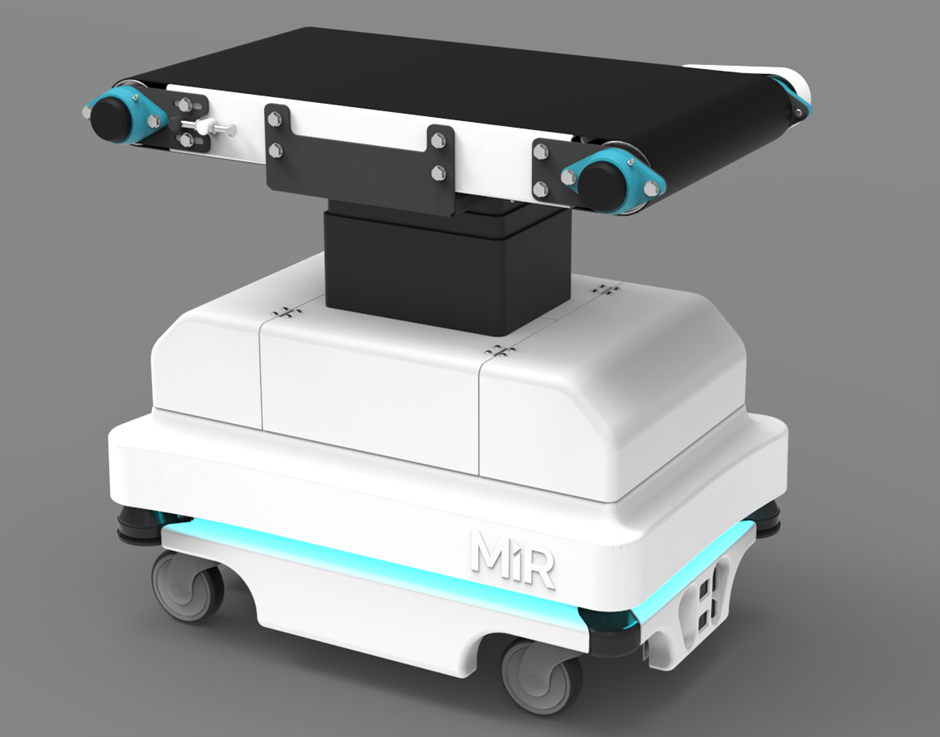
Source: own
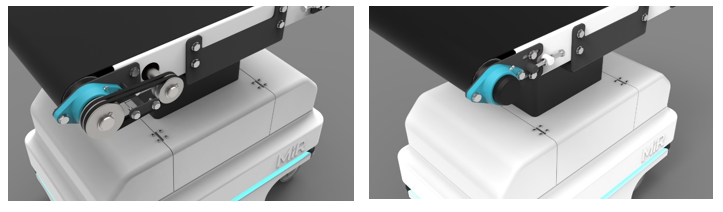
Source: own
Planning, development and design of Soft robotic gripper for collaborative robot UR5e
In the framework of the research field “Logistics technique and technology” and in collaboration with students, a soft robotic gripper for collaborative robot UR5e has been developed, designed and constructed.
Source: own
Source: own
Source: own
Source: own
Source: own
Source: own
Source: own